Quality Management System
QMS Development & Implementation
At EPS Support Services, we specialize in developing and implementing robust Quality Management Systems (QMS) that align with international standards such as ISO 9001, ISO 14001, and ISO 45001 as well as industry-specific quality frameworks.
Our expertise ensures that organizations achieve operational excellence while maintaining compliance with regulatory requirements.
Our comprehensive QMS Development & Implementation services include:
Current State Assessment: Evaluating existing quality management processes to identify strengths, weaknesses, and areas for improvement.
Gap Analysis Against ISO and Industry Standards: Conducting thorough assessments to ensure alignment with international and regional regulatory requirements.
QMS Design and Documentation: Developing a tailored QMS framework, including policies, procedures, and process controls, to streamline business operations.
Implementation Support: Assisting organizations in deploying QMS frameworks, ensuring seamless integration across all departments.
Internal Auditor Training: Providing specialized training programs to equip employees with the necessary skills for conducting internal audits and maintaining compliance.
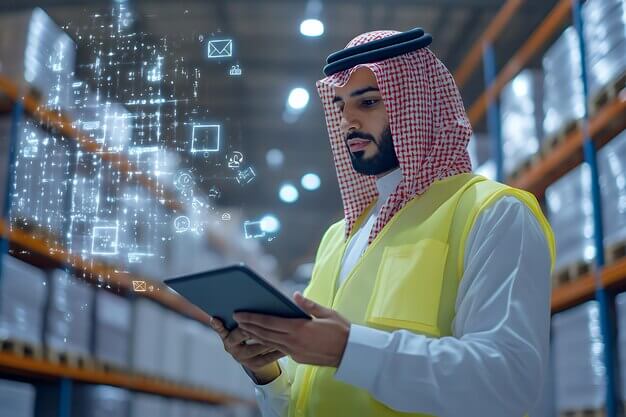
QMS Digitalization
In today’s rapidly evolving business landscape, digital transformation is critical to enhancing efficiency and maintaining a competitive edge.
EPS Support Services assists companies in digitizing their Quality Management Systems to optimize operations and enable real-time data-driven decision-making.
- Process Mapping and Optimization
- Digital Transformation Roadmap Development
- Technology Platform Selection
- Implementation Support
- Integration with Enterprise Systems
- Enhanced transparency and efficiency
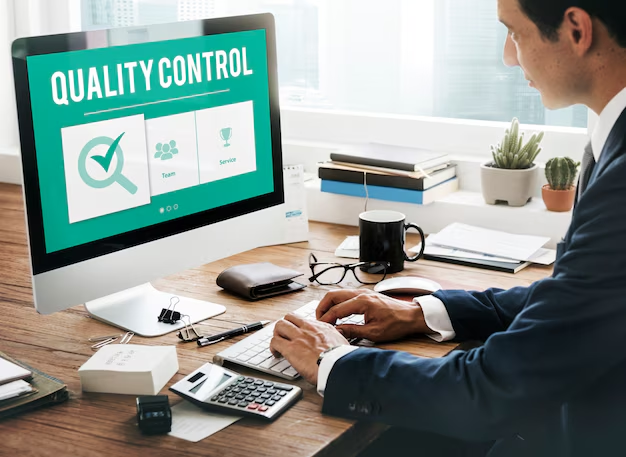
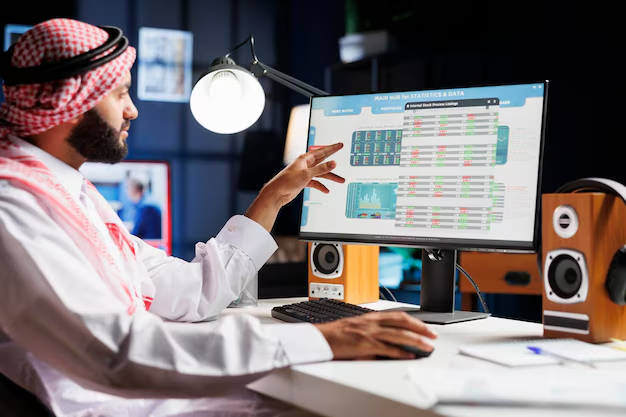
Continuous Improvement Programs
A well-structured continuous improvement strategy is essential for sustaining high-quality standards and operational efficiency.
EPS Support Services offers tailored continuous improvement programs based on global best practices such as Lean, Six Sigma, and Total Quality Management (TQM).
- Lean/Six Sigma Implementation
- KPI Development and Monitoring
- Performance Improvement Methodologies
- Root Cause Analysis Training
- Quality Culture Development
- Demand Forecasting
- Material Coding and Standardization